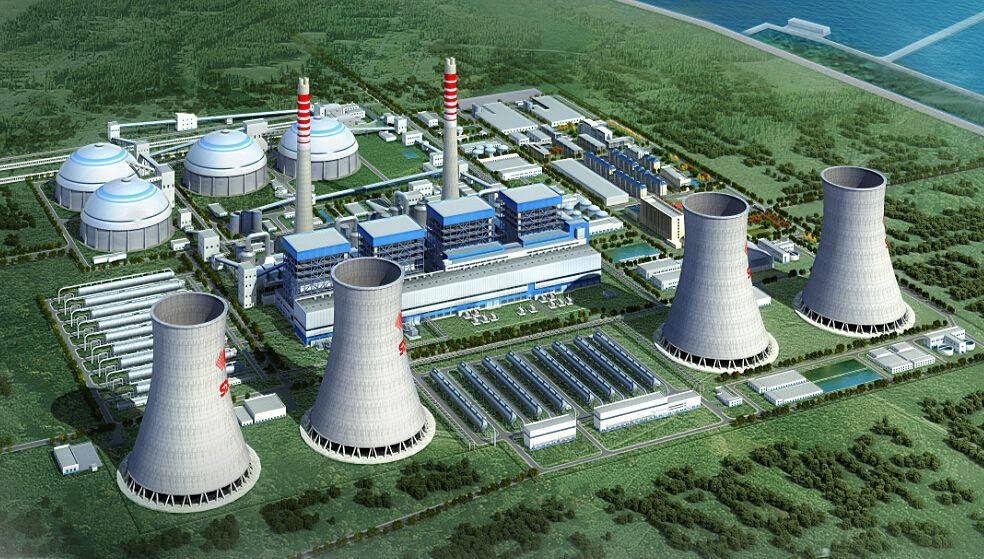
The power plant consists of multiple subsystems such as coal transportation system, combustion system, air supply system, steam system, power generation system, power transmission system, cooling system, ash removal system, etc., which convert heat into electrical energy and discharge the waste heat after power generation.
Absorption heat pump waste heat recovery technology
The waste heat carrier of water-cooled power plants and indirect air-cooled power plants is circulating water, the temperature in winter is only 20-30℃, and the exhaust steam of air-cooled power plants is only about 50℃. This part of heat needs to be heated by a heat pump to heat the hot water network. The absorption heat pump uses the temperature difference in the heating process to do work and realizes zero-energy waste heat recovery, which is very economical. Therefore, this method is widely used.
Especially for the waste heat recovery unit directly using the exhaust steam of air-cooled power plants, the condenser and the absorption heat pump with special structure are integrated, which not only takes into account the need for direct heat exchange of exhaust steam in the early and late cold periods, but also realizes the exhaust steam entering the heat pump evaporator. The waste heat recovery efficiency is very high and has good economy.
The investment in the waste heat recovery technology of absorption heat pump is high, but since it does not change the status quo of the power plant and the driving energy consumption is zero, the overall economic efficiency is good.
Cylinder cutting/high back pressure waste heat recovery technology
The reason why the absorption heat pump is used to recover the waste heat of the steam turbine exhaust steam is that the waste heat temperature is lower than the water temperature of the hot network. If the exhaust steam temperature is increased, the waste heat can be used by direct heat exchange, and the investment is greatly reduced. Cylinder cutting/high back pressure waste heat utilization is this route.
The cylinder cutting route increases the amount of heating steam extraction, and most of the steam can be extracted near the heating steam extraction port, leaving only a small amount of exhaust steam for cooling in the low-pressure cylinder. This method is flexible to adjust, can provide heat on demand, and has low modification costs. It is currently widely used. The high back pressure route increases the back pressure of the steam turbine by replacing the rotor and other methods, and directly heats the hot network water. The disadvantages of this method are high modification costs, inflexible adjustment, and the need to determine electricity by heat, which is suitable for bearing basic loads.
Ejector heat pump recovery technology
Ejector heat pumps use the high-pressure characteristics of heating steam extraction to form low-pressure exhaust steam, produce medium-pressure gas, and then heat the hot network water through a steam-water heat exchanger.
This technology has certain applications in direct air-cooled power plants. However, the ejector device causes changes in flow velocity and pressure due to the shape of the flow channel, and has poor adjustability. It is not suitable for large-scale external fluctuations. The steam pressure and exhaust steam pressure of the power plant are affected by the fluctuation of the power generation load of the power plant, and the heating temperature is affected by the weather. The operating conditions fluctuate violently. The ejector heat pump has poor adaptability and may even have negative efficiency.
Ejector heat pumps are more suitable for use in industrial waste heat recovery projects, with stable working conditions and high efficiency.