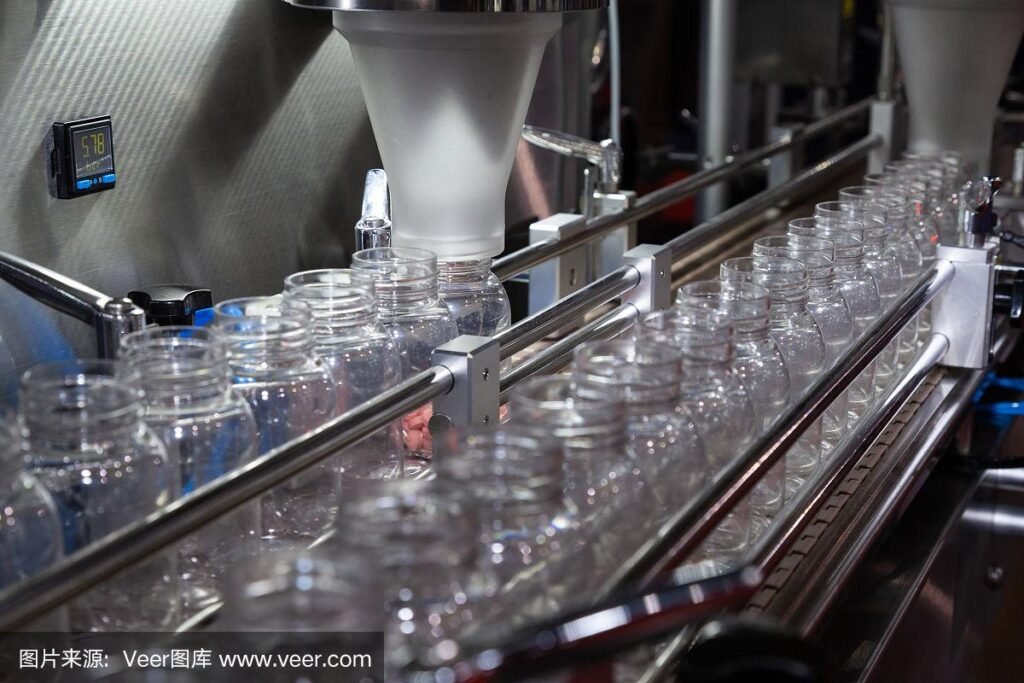
The production of plastic bottles involves multiple links such as injection molding, blow molding, preform heating, and mold temperature control. These processes have very clear demands for heat and cold energy. Traditional heating equipment such as electric heaters and steam boilers have high energy consumption and low efficiency, and cannot fully meet the requirements of modern production for energy efficiency and temperature control accuracy. High-temperature heat pumps, with their advantages of high efficiency, energy saving, precise temperature control, low carbon and environmental protection, have brought significant energy saving effects and process optimization to the plastic bottle production process.
Thermal energy requirements in plastic bottle production
- Preform heating
- Process: Preheat the preform through heating equipment to bring it to the molding temperature.
- Temperature requirements: 80~120°C.
- Heat source requirements: Stable high-temperature heat energy.
- Injection molding process
- Process: The plastic particles are heated and melted, then injected into the mold to form.
- Temperature requirement: 150~300°C (mold temperature controlled at 60~90°C).
- Heat source requirements: High-temperature heat source is used for plastic heating, and medium-temperature heat source is used for mold temperature control.
- Blow molding process
- Process: The heated preform is blow molded by air pressure in the mold.
- Temperature requirements: 80~120°C.
- Heat source requirements: hot air or high temperature hot water.
- Mold temperature control
- Process: Control the mold temperature to ensure dimensional accuracy and surface quality during the molding process.
- Temperature requirements: cooling phase at 1530°C and heating phase at 6090°C.
- Heat source requirements: combined heating and cooling system.
- Scrap recycling
- Process: The leftover materials generated during production are heated, melted and reused.
- Temperature requirements: 150~250°C.
- Heat source requirements: high temperature heat source.
- Cleaning equipment
- Process: Regular cleaning and disinfection of equipment and molds.
- Temperature requirements: 70~90°C.
- Heat source requirement: high temperature hot water.
- Waste heat recovery
- Process: Recover the waste heat emitted by injection molding machines and blow molding machines and use it for preheating or cleaning in other links.
- Heat source requirement: low grade heat energy.
Application scenarios of high-temperature heat pumps in plastic bottle production
- Preform heating
- Application scenario: Provide hot water or hot air at 80~120°C for preheating of preforms.
- Advantages:
- Stable heating and reduce temperature fluctuations;
- Significant energy saving effect, reducing electric heating costs.
- Injection molding heating and mold temperature control
- Application scenario: Provide high-temperature heat energy of 150300°C to heat plastic particles, and provide 6090°C hot water or cooling water for mold temperature control.
- Advantages:
- Precise temperature control to improve product molding quality;
- Heat pump systems meet both heating and cooling needs, reducing the number of equipment.
- Blow molding
- Application scenario: Provide hot air at 80~120°C for the preform blow molding process.
- Advantages:
- Efficient heating to improve blow molding efficiency;
- Uniform temperature control ensures molding accuracy.
- Scrap recycling
- Application scenario: Provide high-temperature heat energy of 150~250°C for scrap melting.
- Advantages:
- Energy saving and environmental protection, improving material utilization;
- Reduce energy consumption of traditional electric heaters.
- Cleaning process
- Application scenario: Provide high-temperature hot water of 70~90°C for equipment and mold cleaning.
- Advantages:
- Better cleaning effect, reducing the use of chemical cleaning agents;
- Savings on fuel costs of conventional boilers.
- Waste heat recovery
- Application scenario: Recover heat energy from the cooling water of injection molding machines and molds to preheat bottle preforms or wash water.
- Advantages:
- Improve overall energy efficiency;
- Reduce additional heat energy requirements.
Case study: High-temperature heat pump renovation project in a plastic bottle factory
Project background
A manufacturer with an annual output of 100 million plastic bottles originally used electric heating equipment and gas boilers to provide heat energy for production, which resulted in high energy consumption and serious waste of heat energy.
Renovation plan
- Use a high-temperature heat pump to provide the required heat energy (80~120°C) for preform heating, injection molding process and mold temperature control;
- Equipped with a waste heat recovery system to dissipate heat from the injection molding machine for preheating of preforms;
- Provide high-temperature hot water of 70~90°C for the cleaning system.
Transformation effect
- Energy-saving benefits: Heat energy costs are reduced by 30%, with annual cost savings of 500,000 yuan;
- Environmental benefits: reduce carbon emissions by approximately 800 tons;
- Production efficiency: Improved mold temperature control accuracy and improved product qualification rate;
- Return on investment: Recover the renovation cost in 1.5 years.
Advantages of high temperature heat pumps in plastic bottle production
- Energy saving and environmental protection
- The heat pump has a high energy efficiency ratio (COP) and reduces operating energy consumption by more than 40%.
- Precise temperature control
- Accurate and stable temperature control improves product quality.
- Flexible integration
- Simultaneous heating and cooling functions are provided to simplify the equipment system.
- Waste heat utilization
- Recover waste heat generated during the production process to further reduce energy consumption.
- Low carbon emissions
- Replace traditional boilers and electric heating equipment to reduce greenhouse gas emissions.
Conclusion: High-temperature heat pumps help green manufacturing in the plastic bottle industry
The application of high-temperature heat pumps in the production of plastic bottles not only effectively reduces production energy consumption, but also improves product quality through precise temperature control. It is an important technical means to promote the industry’s transformation to green manufacturing. In the future, as energy conservation and environmental protection requirements increase, high-temperature heat pumps will become key equipment in the production of plastic bottles and related products. Welcome to consult the professional team to customize your high-efficiency and energy-saving solution!