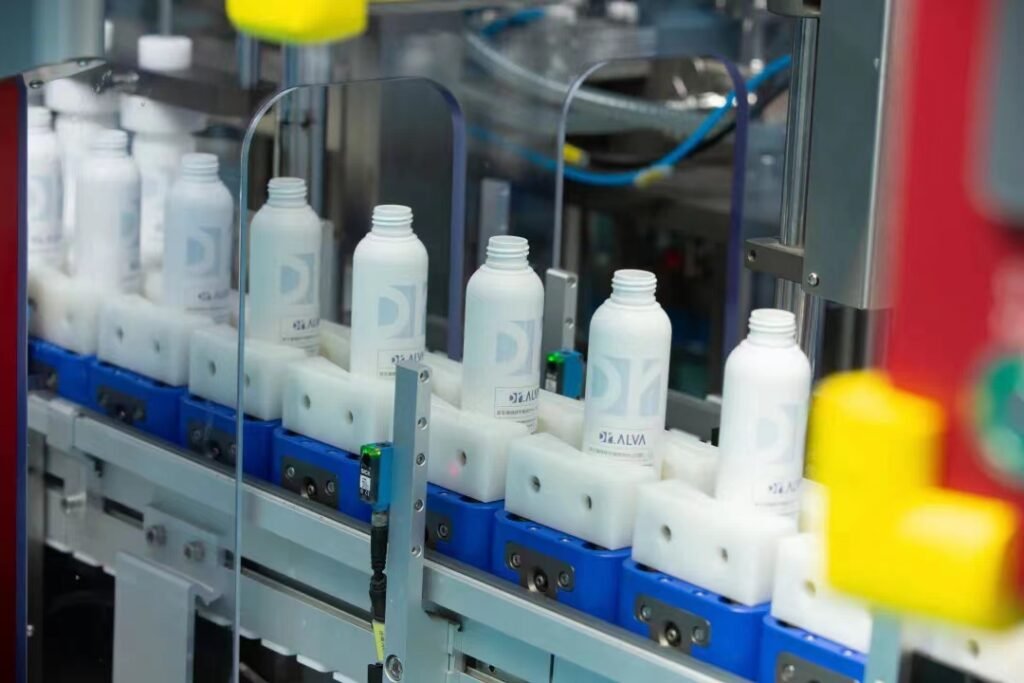
Housewives are a liquid product widely used in oral cleaning and care. Its production involves multiple links such as cleaning, batching, mixing, sterilization, and filling, and has a high demand for heat energy. Traditional heating methods have the problems of high energy consumption and low efficiency. As a highly efficient and energy-saving thermal energy technology, high-temperature heat pumps have shown great application potential in mouthwash production.
Heat energy demand in mouthwash production
- Raw material cleaning
- Process: Clean the containers, batching equipment and water treatment systems used in production.
- Temperature requirement: 50~70°C (hot water cleaning).
- Heat source requirement: low-temperature hot water.
- Ingredient dissolution
- Process: Dissolve or mix the main ingredients such as glycerin, plant extracts, etc. evenly.
- Temperature requirement: 40~60°C.
- Heat source requirement: stable hot water or heating equipment.
- Mixing and homogenization
- Process: Mix the ingredients thoroughly by heating and stirring to form a stable liquid.
- Temperature requirement: 50~70°C.
- Heat source requirement: medium-temperature hot water or steam.
- Sterilization
- Process: Ensure the hygienic safety of the gargle through pasteurization or high-temperature sterilization.
- Temperature requirement: 80~100°C.
- Heat source requirement: high-temperature hot water or hot steam.
- Cleaning and disinfection
- Process: Regularly clean and disinfect production equipment and pipelines at high temperature.
- Temperature requirement: 80~90°C.
- Heat source requirement: high-temperature hot water.
- Waste heat recovery
- Process: Recover the waste heat generated during sterilization and cleaning for preheating water or other processes.
- Temperature requirement: low-grade waste heat.
Application scenarios of high-temperature heat pumps in gargle production
- Cleaning process
- Application scenario: Provide 50~70°C hot water for equipment cleaning.
- Advantages:
- Replace the traditional boiler system and significantly reduce the cost of hot water;
- Constant temperature and improve cleaning efficiency.
- Batching and dissolving
- Application scenario: Provide 40~60°C hot water for raw material dissolution.
- Advantages:
- The heat pump has precise temperature control to ensure complete and uniform dissolution of the ingredients;
- Significant energy saving effect and reduced operating costs.
- Mixing heating
- Application scenario: Provide stable medium-temperature hot water for the mixing process.
- Advantages:
- Stable heating to avoid temperature fluctuations during the mixing process;
- Reduce energy waste of traditional heating equipment.
- Sterilization and disinfection
- Application scenario: Provide 80~100°C high-temperature hot water for sterilization.
- Advantages:
- High-temperature heat pumps can achieve precise temperature control to ensure sterilization effects;
- Replace steam boilers to reduce carbon emissions.
- Waste heat recovery
- Application scenario: Recover waste heat discharged during sterilization and cleaning for preheating cleaning water.
- Advantages:
- Improve energy utilization efficiency;
- Reduce overall energy consumption.
Case Analysis: High-temperature heat pump renovation project of a gargle factory
Project background
A manufacturer with an annual output of 2,000 tons of gargle originally used gas boilers to provide heat energy for the production process, which was costly and inefficient, and there were steam leaks and pipeline heat losses.
Renovation plan
- Introduce a high-temperature heat pump system to provide 40-100°C hot water for cleaning, dissolving, mixing and sterilization;
- Set up a waste heat recovery device to use the waste heat released during the production process to preheat the cleaning water;
- Optimize the existing pipeline system to reduce heat loss.
Renovation effect
- Energy saving benefits: save about 350,000 yuan in energy costs per year;
- Environmental benefits: reduce carbon dioxide emissions by about 700 tons;
- Production benefits: improve thermal energy stability and increase production efficiency by 10%;
- Return on investment: recover the renovation cost within 1.8 years.
Advantages of high-temperature heat pumps in the production of gargles
- High efficiency and energy saving
- The energy efficiency ratio is as high as 4.0~5.0, which saves more than 40% energy compared with traditional boiler systems.
- Precise temperature control
- Meet the temperature control requirements of different processes and ensure stable product quality.
- Environmentally friendly
- Reduce the use of fossil fuels, achieve low-carbon production, and meet green manufacturing standards.
- Multifunctional integration
- One machine for multiple uses, meeting the thermal energy requirements of multiple links such as cleaning, heating, and sterilization.
- Waste heat recovery
- Recover waste heat for other processes to further improve energy utilization.
- Stable operation
- The heat pump system has a high degree of automation and low operating and maintenance costs.
Conclusion: High-temperature heat pumps promote the green upgrade of gargle production
The application of high-temperature heat pump technology in gargle production not only optimizes thermal energy management and improves production efficiency, but also helps companies achieve energy conservation and emission reduction goals. With the increase in the industry’s demand for green manufacturing, high-temperature heat pumps will play a greater role in the production of gargles and other daily chemical products. Welcome to contact our professional team to provide efficient and energy-saving heat pump solutions for your production line!