High-temperature heat pumps can effectively improve energy utilization efficiency, reduce production costs, and optimize production processes in quilt production. Quilt production involves multiple high-energy-consuming links, such as cotton drying, shaping, compression and packaging. High-temperature heat pumps can provide ideal heat sources and temperature control solutions for these processes through waste heat recovery and efficient heating.
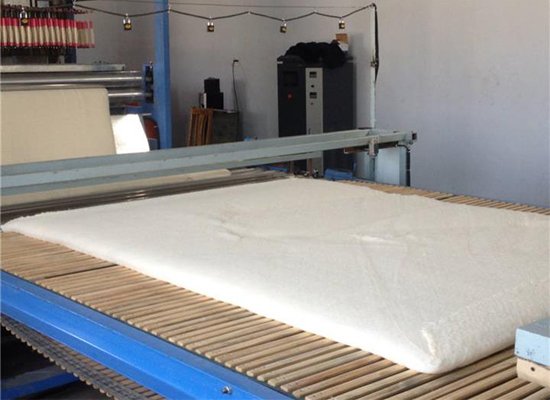
Key processes and heat pump application points in quilt production
- Cotton drying
- Raw cotton needs to be dried before production to remove moisture for subsequent processing.
- Traditional drying equipment mostly relies on steam or gas heating, which consumes a lot of energy.
- High-temperature heat pumps can recover waste heat and provide 60~100°C hot air for cotton drying, reducing fuel consumption.
- Hot air shaping
- Quilts need to be heated and shaped during sewing and shaping to ensure shape stability and comfort.
- Heat pumps provide constant temperature hot air (80~120°C), replacing traditional boilers or electric heating, with higher stability.
- Compression packaging
- Before packaging, cotton quilts need to be heat treated to remove some moisture to prevent mold after packaging.
- High-temperature heat pumps provide the required heat source for compression packaging through precise temperature control.
- Production waste heat recovery
- Waste heat sources in cotton quilt production, such as drying exhaust gas, waste heat steam, etc., can be recovered through the heat pump system for heating or other processes.
Actual case
A cotton quilt factory heat pump energy-saving transformation project
Project background
The annual output of the cotton quilt factory is 2 million cotton quilts. The production process includes cotton drying, hot air shaping and other links. The energy mainly relies on gas boilers and electric heating equipment. The production cost is high and there is a problem of waste heat waste.
Transformation content
- Introduce a high-temperature heat pump system to replace boilers and some electric heating equipment.
- Install a heat pump hot air circulation system in the cotton drying section to recover waste heat exhaust gas and heat it to 80~90°C for drying.
- Add a high-temperature heat pump to provide precise constant-temperature hot air (100°C) in the hot air shaping process.
- Install a heat pump waste heat recovery module at the exhaust gas discharge end to convert low-grade heat energy into high-temperature heat energy for other processes.
Application effect
- Energy saving
- The energy efficiency of the drying process is improved by about 40%;
- Replacing boilers saves about 300,000 cubic meters of natural gas per year;
- Total electricity consumption is reduced by about 15%.
- Economic benefits
- Initial investment: about 2 million yuan;
- Annual cost savings: about 700,000 yuan;
- Payback period: 2.8 years.
- Environmental benefits
- Annual reduction of carbon dioxide emissions by about 500 tons;
- Reduce exhaust gas emissions and improve air quality in the factory area.
- Improved production efficiency and product quality
- More precise temperature control to ensure uniform drying of quilts and improve product quality;
- Drying time is shortened by 20% to improve production efficiency.
Advantages Summary
- Energy saving and emission reduction: The heat pump system has high comprehensive energy efficiency, significantly reducing energy consumption and carbon emissions.
- Low operating cost: Through waste heat recovery and efficient heat pump operation, electricity and fuel costs are reduced.
- High temperature control accuracy: Ensure the processing quality of quilts and reduce production scrap rate.
- Environmental compliance: Comply with clean production and energy-saving and environmental protection policies, and help enterprises transform green.
If you want to explore the technical implementation or investment return analysis of heat pumps in similar application scenarios in more depth, I can provide further detailed solutions!