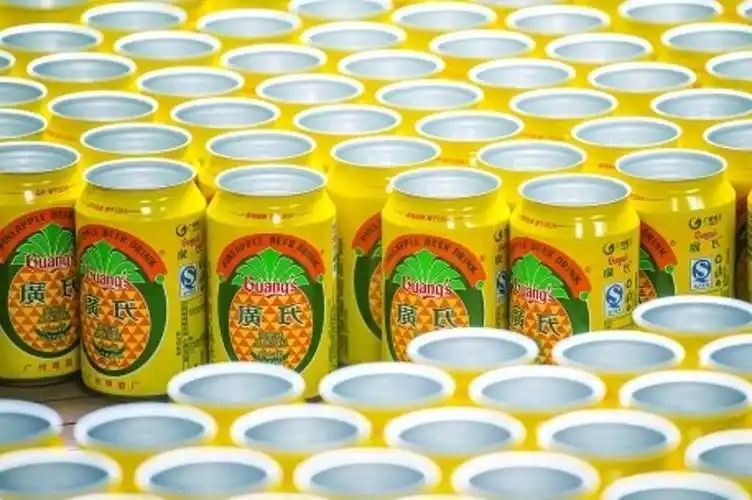
Pineapple beer is a fruit-flavored beer. Its production combines the process of juice processing and beer fermentation, and involves multiple thermal energy links that require precise temperature control, such as juice concentration, sterilization, enzymatic hydrolysis, and cleaning. Traditional heat source equipment such as gas boilers and electric heaters have high energy consumption and limited temperature control accuracy. High-temperature heat pump technology has brought significant energy saving and quality improvement to pineapple beer production with its advantages of high efficiency, environmental protection and precise temperature control.
Heat requirements in pineapple beer production
- Raw material cleaning
- Process: Clean and decontaminate pineapple raw materials.
- Temperature requirements: 40~60°C.
- Heat source requirements: warm water for cleaning.
- Juice concentrate
- Process: Pineapple juice is concentrated by heating so it can be mixed with the beer base.
- Temperature requirements: 60~90°C.
- Heat source requirements: medium temperature hot water or steam.
- Enzymatic hydrolysis process
- Process: Heating is used to promote the activity of enzymes to break down the components in pineapple juice.
- Temperature requirements: 50~70°C.
- Heat source requirements: Constant temperature heat source.
- Sterilization treatment
- Process: Pasteurizes juices and mixes to ensure food safety.
- Temperature requirements: 80~100°C.
- Heat source requirement: high temperature hot water or steam.
- Fermentation temperature control
- Process: Control the temperature of the beer fermentation process, usually between 5 and 25°C.
- Temperature requirements: cryogenic cooling.
- Heat source requirements: waste heat recovery or refrigeration.
- Equipment cleaning (CIP system)
- Process: High-temperature cleaning and disinfection of production equipment.
- Temperature requirements: 80~90°C.
- Heat source requirement: high temperature hot water.
- Waste heat recovery
- Process: Recover the waste heat generated during concentration and sterilization for use in other links.
- Heat source requirement: low grade heat energy.
Application scenarios of high-temperature heat pumps in pineapple beer production
- Juice concentrate
- Application scenario: Provide 60~90°C hot water for the concentration process.
- Advantages:
- Stable heat supply to ensure uniform concentration of juice;
- Significant energy saving effect, reducing production costs.
- Enzymatic hydrolysis and sterilization
- Application scenario: Provide 50~100°C hot water for enzymatic hydrolysis reaction and sterilization process.
- Advantages:
- High-temperature heat pump can achieve precise temperature control and ensure the efficiency of enzymatic hydrolysis reaction;
- Stable sterilization temperature ensures product hygiene and safety.
- Equipment cleaning
- Application scenario: Provide 80~90°C high temperature hot water for equipment cleaning and disinfection.
- Advantages:
- Replace traditional boilers to reduce energy consumption and carbon emissions;
- Improve cleaning efficiency and reduce downtime.
- Waste heat recovery
- Application scenario: Recover waste heat from the juice concentration and sterilization process for preheating cleaning water or fermentation temperature control.
- Advantages:
- Improve energy efficiency;
- Reduce overall heat energy requirements.
Case study: High-temperature heat pump renovation project of a pineapple brewery
Project background
A factory with an annual output of 5,000 tons of pineapple beer originally used gas boilers and electric heating equipment to provide heat energy for the production process. The heat energy utilization rate was low and the energy consumption cost was high.
Renovation plan
- Introduce a high-temperature heat pump system to provide the required heat energy (50~100°C) for juice concentration, sterilization, enzymatic hydrolysis and cleaning processes;
- Set up a waste heat recovery device to use the waste heat from the concentration and sterilization processes for washing water preheating and fermentation temperature control;
- Replace part of the cooling system and use the heat pump for low-temperature cooling.
Transformation effect
- Energy-saving benefits: Heat energy costs are reduced by 40%, and annual operating expenses are saved by 600,000 yuan;
- Environmental benefits: reduce carbon dioxide emissions by approximately 1,200 tons;
- Production efficiency: temperature control accuracy is improved, and the juice loss rate during concentration is reduced by 5%;
- Return on investment: Recover the renovation cost within 1.6 years.
Advantages of high temperature heat pump in pineapple beer production
- Energy saving and high efficiency
- The heat pump energy efficiency ratio (COP) is as high as 4.0~5.0, significantly reducing energy consumption.
- Precise temperature control
- Meet the requirements for different process temperatures during pineapple beer production and improve product quality.
- Environmentally friendly
- Reduce boiler usage and carbon emissions, complying with green production standards.
- Waste heat utilization
- Maximize waste heat recovery during production and improve overall energy utilization.
- Reduce operating costs
- Replace traditional energy equipment, saving energy costs and maintenance costs.
- Multifunctional integration
- Meets heating and cooling needs simultaneously, simplifying equipment layout.
Conclusion: High-temperature heat pumps help the sustainable development of the pineapple beer industry
The application of high-temperature heat pump technology in pineapple beer production not only meets the diverse demands for heat energy in the production process, but also helps the company achieve energy conservation and emission reduction goals. With the further promotion of green manufacturing concepts, high-temperature heat pumps will become an important technical support for the production of pineapple beer and other food and beverages. Welcome to contact the professional team to customize an energy-saving transformation plan for your production line and jointly promote the sustainable development of the industry!