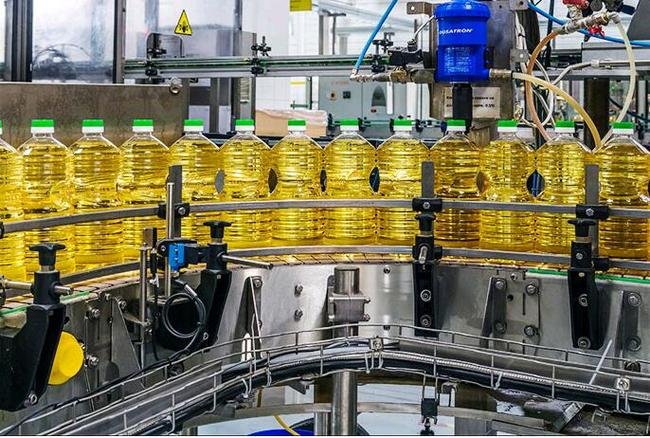
The peanut oil production process involves multiple links such as cleaning, steaming, pressing, and refining. The demand for heat energy in each link accounts for a large proportion of the total production cost. At the same time, a large amount of low-grade waste heat is emitted during the production process. High-temperature heat pumps can efficiently recycle waste heat, raise it to a high temperature, and then use it in steaming, deacidification, deodorization, and equipment cleaning, which can significantly reduce energy consumption and improve production efficiency.
Main heat-consuming links in peanut oil production
- Raw material cleaning
- Process: Peanuts are washed to remove dirt and impurities.
- Temperature requirement: cleaning water temperature 40~60°C.
- Steam and stir-fry
- Process: Steam and fry the peanuts to a certain temperature to increase the oil extraction rate.
- Temperature requirement: generally 90~120°C.
- Squeeze
- Process: Groundnuts are pressed under high temperature to extract crude oil.
- Temperature requirements: Appropriate heating state, about 100°C, is required before pressing.
- Refining
- Process: It includes several refining steps such as degumming, deacidification, decolorization and deodorization.
- Temperature requirements:
- Deacidification: 120~140°C.
- Deodorization: 200~240°C.
- Heat sources are mainly used to heat and maintain high temperatures.
- Equipment cleaning
- Process: Production equipment requires regular high temperature cleaning and disinfection.
- Temperature requirement: cleaning water temperature 60~90°C.
- Waste heat discharge
- Source: Waste heat emitted from the steaming and refining stages (temperature about 50~80°C), and waste water heat from the washing stage.
Application scenarios of high temperature heat pumps
- Recovery of waste heat from steaming and frying
The waste heat from steam condensation (temperature of about 60~80°C) generated during the steaming and frying process can be recovered by a high-temperature heat pump and raised to 90~120°C for subsequent steaming and frying or pressing processes.
- Utilization of waste heat from refining
The heat emitted from the refining process (deacidification, deodorization, etc.) can be heated to the required process temperature (such as 120~240°C) through a high-temperature heat pump to provide thermal energy support for other refining steps.
- Cleaning waste heat recovery
The heat energy (40~60°C) of wastewater discharged from equipment cleaning is recovered through a high-temperature heat pump and can be used to heat a new round of cleaning water or to preheat raw material cleaning water.
- Thermal energy integration management
The high-temperature heat pump system can centrally recover the low-temperature waste heat from each production link, and distribute it to the steaming, refining, cleaning and other links after heating, to build an efficient thermal energy circulation system.
Economic and environmental benefits
- Energy saving and consumption reduction
- High temperature heat pumps recover waste heat to replace traditional coal-fired boilers or gas-fired boilers, significantly reducing energy consumption.
- The energy efficiency ratio (COP) is as high as 3~5, and 3~5kW of heat energy can be output for every 1kW of electricity consumed.
- Reduce operating costs
- High temperature heat pumps are cheaper to operate than conventional boilers, saving fuel and maintenance costs.
- Reduce carbon emissions
- Reducing the use of fossil fuels and lowering emissions of carbon dioxide and other pollutants will help companies achieve carbon neutrality goals.
- Improve production efficiency
- High temperature heat pumps provide stable, precise heat to ensure continuity and high quality of production processes.
Case Study
Background data:
- A peanut oil factory produces 200 tons per day.
- Steaming and frying require 1,500 kW of heat, and refining requires 2,000 kW of heat.
- Waste heat discharge (temperature 60~80°C) is about 2,000 kW.
Energy consumption calculation:
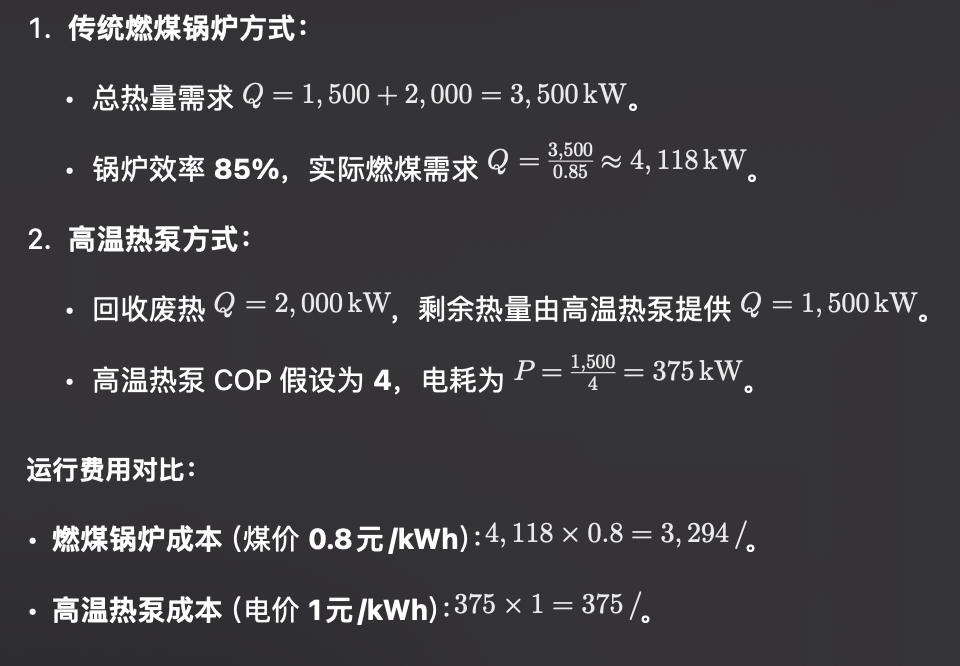
Savings:
The cost savings per hour is , 20 hours of operation per day, 300 days of operation per year, and the annual cost savings are:

Carbon reduction:
Reduce coal consumption by 3,743 kW. Based on the coal carbon emission factor of 0.7 kg COâ‚‚/kWh, the annual emission reduction is:

in conclusion
The application of high-temperature heat pumps in peanut oil production significantly reduces the heat demand and operating costs of steaming, refining and equipment cleaning by efficiently recovering and utilizing waste heat in the production process. At the same time, reducing carbon emissions and helping companies achieve green production goals are important means to promote energy conservation and emission reduction in the traditional edible oil production industry.