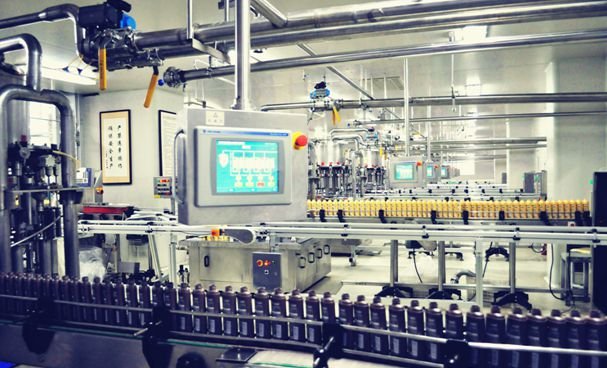
The shampoo production process includes raw material heating, stirring and mixing, emulsification, sterilization, filling and other links, many of which require a large amount of heat energy. In addition, a large amount of low-grade waste heat (such as wastewater and waste gas heat) will be generated during the production process. High-temperature heat pumps can meet the heat energy needs of different processes by recycling and utilizing these waste heats, while reducing production costs and carbon emissions.
Main heat-using processes for shampoo production
- Raw material heating
- Process: Heat raw materials such as base oil, surfactant, thickener, etc. to achieve a suitable liquid state for subsequent mixing.
- Temperature requirement: Usually 60~80°C.
- Stirring and emulsification
- Process: Mix the heated raw materials evenly in the stirring tank and form a stable emulsion through the emulsification process.
- Temperature requirement: A stable temperature of 70~90°C needs to be maintained.
- Sterilization
- Process: High-temperature sterilization of the emulsion before filling to ensure product quality.
- Temperature requirement: usually 100~120°C.
- Cleaning and disinfection
- Process: Production equipment needs to be cleaned and disinfected with high-temperature water after batch switching or production.
- Temperature requirement: The temperature of cleaning water is usually 60~90°C.
- Wastewater treatment
- Process: Wastewater discharged during the production process needs to be treated, and some wastewater contains usable heat energy.
- Temperature requirement: The temperature of wastewater is usually 40~60°C.
Application scenarios of high-temperature heat pumps
- Raw material heating and mixing
High-temperature heat pumps can recover the heat of wastewater (temperature 40~60°C) in the shampoo production process and raise it to 70~90°C for heating raw materials and mixing kettle temperature control.
- Effect: Significantly reduce the energy consumption of coal-fired boilers or electric heating equipment.
- Sterilization heat recovery
In the sterilization process, the high-temperature steam used generates condensation waste heat with a temperature of about 70~90°C. High-temperature heat pumps can raise these waste heat to 100~120°C and supply them to sterilization equipment again.
- Case: Through the heat pump system, the heat energy in the sterilization process can be closed-loop utilized.
- Recycling of cleaning water
The temperature of hot water discharged from the cleaning equipment is usually 50~70°C. The high-temperature heat pump can heat it to 90°C for re-cleaning or heating in other links.
- Effect: Reduce the demand for boiler hot water and improve the utilization rate of water resources.
- Comprehensive thermal energy management
Shampoo production plants can integrate waste heat resources from various links through the central high-temperature heat pump system, and centrally recover low-temperature waste heat and supply it to the required process links (such as heating, sterilization, cleaning, etc.).
- Effect: Improve energy utilization efficiency and realize the cascade utilization of thermal energy.
Economic and environmental benefits
- Reduce energy consumption
- Traditional production methods rely on coal-fired or natural gas boilers to provide heat energy, and the operating cost is relatively high.
- High-temperature heat pumps use waste heat for heating, with a COP of 3.0~5.0, significantly reducing energy consumption.
- Reduce carbon emissions
- Reduce COâ‚‚ emissions by reducing boiler fuel use, helping companies achieve carbon neutrality goals.
- Save operating costs
- High-temperature heat pumps can reduce the operating costs of steam boilers or electric heating, reducing production costs.
- Improve production stability
- The heat output of high-temperature heat pumps is stable and controllable, which helps to ensure the temperature control accuracy of the production process, thereby improving product quality.
Case analysis
Background data:
- The factory produces 50 tons of shampoo per day.
- The heat required for heating raw materials and sterilization processes is 1,200 kWh/batch (3 batches per day).
- The available heat from production waste heat (wastewater temperature 50°C) is about 600 kWh/batch.
Energy consumption comparison:
- Traditional method:
- Use coal-fired boilers to provide the required heat.
- The heat demand per batch is 1,200 kWh, the efficiency of the coal-fired boiler is about 85%, and the actual fuel consumption is 1,412 kWh/batch.
- High-temperature heat pump method:
- 600 kWh/batch of wastewater heat is recovered, and the remaining 600 kWh of heat is provided by the heat pump.
- The COP of the heat pump is 4.0, and the power consumption is 150 kWh/batch.
Operation cost comparison:
- Coal-fired boiler: The fuel cost per batch (based on the coal price of 0.8 yuan/kWh) is 1,129 yuan.
- High-temperature heat pump: The electricity cost per batch (based on the electricity price of 1 yuan/kWh) is 150 yuan.
Savings:
The daily cost savings are approximately (1,129 – 150) × 3 = 2,937 yuan.
Conclusion
The application of high-temperature heat pumps in shampoo production not only effectively reduces production costs and carbon emissions, but also improves the energy efficiency of the production line by recycling waste heat resources for raw material heating, sterilization and cleaning processes. With the increasing requirements for energy conservation and emission reduction, high-temperature heat pumps will become an important tool for the shampoo production industry to achieve green production.