The production process of instant noodles involves multiple heat energy demand links, including cooking, frying, drying, seasoning mixing, and equipment cleaning. Traditional heating methods such as gas boilers and electric heaters have problems such as high energy consumption and low efficiency. As an efficient heat energy conversion technology, the application of high-temperature heat pumps in instant noodle production can effectively improve energy efficiency, reduce operating costs, and optimize production processes.
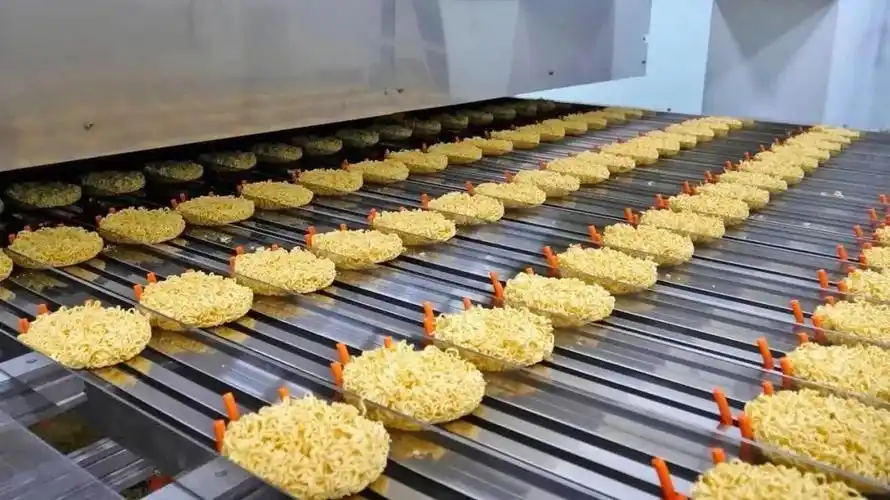
Heat energy demand in instant noodle production
- Noodle cooking
- Process: Boil the noodles in hot water to ensure that the noodles reach the appropriate softness and hardness.
- Temperature requirement: 90~100°C.
- Heat source requirement: high-temperature hot water.
- Frying process
- Process: Fry the boiled noodles in a fryer to increase their crispness.
- Temperature requirement: 160~180°C.
- Heat source requirement: high-temperature oil or steam.
- Seasoning mixing
- Process: Mix the seasoning with the fried noodles evenly.
- Temperature requirement: 30~40°C (to maintain the fluidity of the seasoning).
- Heat source requirement: stable low-temperature heating.
- Drying and drying
- Process: Further dry the fried noodles to remove excess moisture.
- Temperature requirement: 80~120°C.
- Heat source requirement: medium-high temperature hot air or hot water.
- Equipment cleaning
- Process: Regularly clean the frying equipment, boilers and pipes to ensure production hygiene.
- Temperature requirement: 70~90°C.
- Heat source requirement: high-temperature hot water.
- Waste heat recovery
- Process: Recover waste heat from frying and drying processes for preheating water or other links.
- Heat source requirement: low-grade heat source.
Application scenarios of high-temperature heat pumps in instant noodle production
- Noodle cooking
- Application scenario: High-temperature heat pumps provide 90~100°C hot water for the cooking process.
- Advantages:
- High-temperature heat pumps replace traditional boilers to provide hot water, saving energy;
- Reduce temperature fluctuations to ensure consistent noodle cooking results.
- Frying process
- Application scenario: Provide 160~180°C hot oil for frying process.
- Advantages:
- Efficiently provide heat energy, with significant energy-saving effect;
- Stable high-temperature oil keeps instant noodles crispy and improves production efficiency.
- Seasoning mixing
- Application scenario: Provide a stable heat source of 30~40°C for seasoning mixing.
- Advantages:
- Maintain the fluidity of seasonings and ensure uniform mixing;
- Avoid energy waste of traditional electric heating.
- Drying and drying
- Application scenario: Provide 80~120°C hot air or hot water for the drying process.
- Advantages:
- High-temperature heat pumps can provide a stable heat source and improve drying efficiency;
- Helps improve product quality and reduce drying time.
- Equipment cleaning
- Application scenario: Provide hot water at 70~90°C for the cleaning process.
- Advantages:
- Improve cleaning efficiency and reduce cleaning time;
- Replace boiler system and reduce energy consumption.
- Waste heat recovery
- Application scenario: Recover waste heat from frying and drying processes for preheating cleaning water or other processes.
- Advantages:
- Improve energy utilization and reduce energy consumption;
- Reduce dependence on external heat sources.
Case analysis: High-temperature heat pump transformation project of a certain instant noodle production enterprise
Project background
A production enterprise with an annual output of 50 million packs of instant noodles uses traditional gas boilers and electric heating equipment to provide heat energy for production. The energy cost is high, and it faces problems such as inaccurate temperature control and low production efficiency.
In the production of instant noodles, recovering waste heat from wastewater and using high-temperature heat pumps to heat it to a higher temperature (for example, from 60°C to 120°C) is an important means to improve energy efficiency and reduce external energy demand. Below we will analyze this process in detail and calculate the required heating capacity.
Prerequisites
- Wastewater temperature: 60°C
- Target temperature: 120°C
- Wastewater flow rate: Assume that the wastewater flow rate is 5 tons/hour (5000 kg/h)
- Heat pump efficiency (COP value): Assume that the COP of the high-temperature heat pump is 4.5 (that is, for every 1 kW of electrical energy consumed, it can provide 4.5 kW of heat energy).
- Specific heat capacity: The specific heat capacity of water is 4.18 kJ/kg·°C.
This means that the heat required to heat 5000 kg/h of wastewater from 60°C to 120°C is 1,254,000 kJ/h or 1,254 MJ/h.
The thermal efficiency (COP) of the high-temperature heat pump is 4.5, that is, for every 1 kW of electrical energy input, it can provide 4.5 kW of heat. We need to calculate the electrical energy required to obtain the required heat (heating capacity / COP).
To heat the wastewater from 60°C to 120°C, the high-temperature heat pump consumes 77.4 kW of electrical energy.
Assuming the electricity price is 0.6 yuan/kWh, the electricity cost per hour is: 46.44 yuan/h
If waste heat is not recovered, traditional heating equipment (such as electric heating or steam boiler) is needed to provide the same heat. Assuming the efficiency of traditional heating equipment is 80%, the required electricity is: 435.42 kW to provide the same heat, and the electricity cost is: 261.65/h;
The waste heat of wastewater is recovered by high-temperature heat pump, and the wastewater at 60°C is heated to 120°C. The required heating capacity is 1,254,000 kJ/h or 1,254 MJ/h, and the electricity consumed is 77.4 kW. Compared with traditional heating methods, 358.02 kW of electricity and 214.81 yuan of electricity cost are saved per hour.
By recycling waste heat and effectively utilizing high-temperature heat pumps, instant noodle manufacturers can not only significantly reduce energy consumption, but also significantly reduce production costs and improve overall energy efficiency.
Advantages of high-temperature heat pumps in instant noodle production
- Energy saving and high efficiency
- The energy efficiency ratio (COP) of high-temperature heat pumps is as high as 4.0~5.0, which can significantly reduce energy consumption.
- Accurate temperature control
- High-temperature heat pumps can provide precise heat sources for each link in the production process to ensure consistent noodle quality.
- Multifunctional integration
- High-temperature heat pump systems can provide high-temperature and low-temperature heat sources at the same time to meet the needs of multiple production links.
- Environmentally friendly
- Reduce the use of traditional boilers and electric heating equipment, reduce carbon emissions, and meet green production standards.
- Waste heat utilization
- The heat pump system can recycle waste heat in the production process and improve overall energy efficiency.
- Reduce operating costs
- Help companies reduce long-term operating costs through efficient thermal energy utilization and low maintenance costs.
Conclusion: High-temperature heat pumps promote the green transformation of instant noodle production
The application of high-temperature heat pump technology in instant noodle production not only improves production efficiency and reduces energy consumption, but also promotes the industry to develop in a green and low-carbon direction. With the continuous improvement of environmental protection requirements, high-temperature heat pumps will become one of the key technologies in instant noodle production. Welcome to consult a professional team to provide customized energy-saving transformation solutions for your instant noodle production line, and jointly achieve green manufacturing and sustainable development!