High-temperature heat pumps can also play an important role in red wine production, especially in fermentation temperature control, wine cellar environment control and waste heat recovery. Through efficient heat management, energy efficiency can be improved, production costs can be reduced, and sustainable development goals can be achieved. The following is a typical application case.
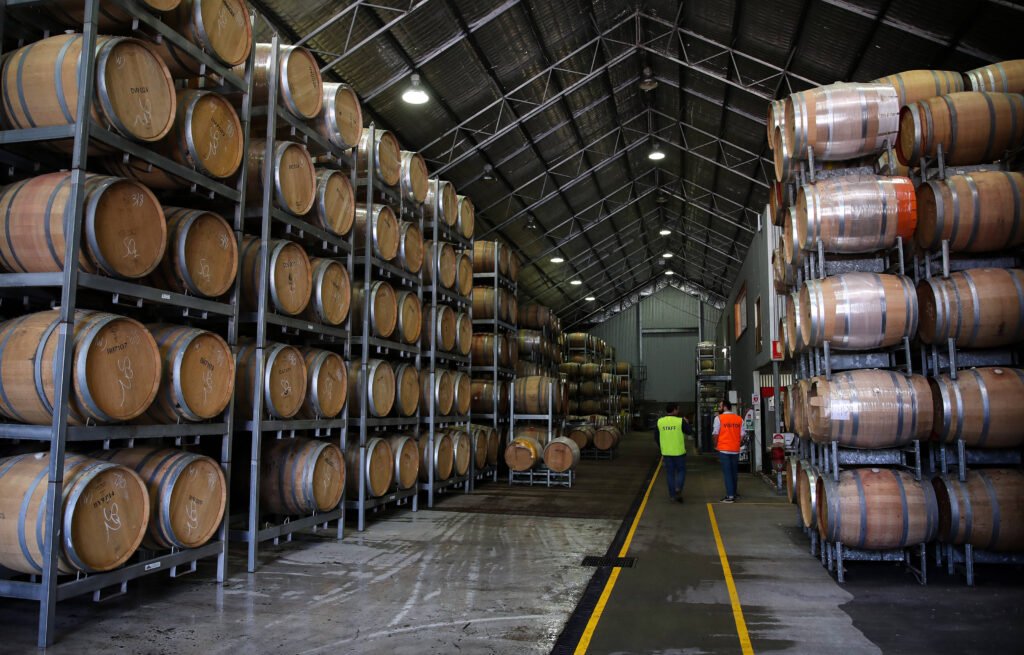
Key processes and heat pump application points in red wine production
- Fermentation temperature control
- Red wine fermentation requires precise temperature control (usually 20~30°C) to maintain yeast activity and fermentation effect.
- High-temperature heat pumps can achieve constant temperature fermentation and provide precise temperature control for fermentation by absorbing waste heat from other links.
- Constant temperature and humidity control of wine cellars
- The ideal storage conditions in wine cellars are usually 1216°C and 6070% humidity.
- High-temperature heat pumps can provide moderate heating for wine cellars in winter, and achieve constant temperature and humidity effects through condensation dehumidification in summer.
- Heating of cleaning water
- Red wine production equipment needs to be cleaned frequently, and high-temperature heat pumps can provide hot water at 60~90°C to replace traditional gas boilers or electric heating devices.
- Waste heat recovery
- A large amount of low-grade waste heat (such as cooling water or process waste heat) is generated during the winemaking process.
- Heat pumps can recover this waste heat for hot water production or space heating.
Actual case
Heat pump renovation project of a winery
Project background
The winery produces 1 million bottles of high-quality red wine annually. The following problems exist in production:
- The fermentation temperature control system consumes a lot of electricity in summer;
- The heating of the wine cellar relies on gas boilers in winter, which is costly;
- The cleaning water is mainly heated by electricity, which is inefficient.
Renovation content
- Install a high-temperature heat pump system for the following links:
- Fermentation tank temperature control: Provide cooling and heating functions through heat pumps to accurately maintain the fermentation temperature;
- Wine cellar environment control: Provide constant temperature and humidity solutions;
- Provide high-temperature cleaning water: The heat pump produces 85°C hot water to replace the original electric heating system.
- Add a waste heat recovery module to recover waste heat from the fermentation tank and condensing equipment to further improve the efficiency of the heat pump.
Application effect
- Energy saving
- Heat pump system COP (coefficient of performance): 4.5
- After replacing the original gas boiler, it saves about 120,000 cubic meters of natural gas per year;
- After replacing electric heating, it saves about 100,000 kWh of electricity per year.
- Economic benefits
- Total investment: about 1.5 million yuan;
- Annual operating cost savings: about 500,000 yuan;
- Payback period: about 3 years.
- Environmental benefits
- Annual reduction of carbon dioxide emissions by about 300 tons, in line with the winery’s green and sustainable development concept.
- Product quality improvement
- The precise temperature control system significantly improves the fermentation efficiency and the quality stability of the finished wine.
Advantages summary
- Energy saving and consumption reduction: Reduce comprehensive energy consumption through waste heat recovery and efficient operation of heat pumps.
- Strong stability: High temperature control accuracy to ensure the consistency of fermentation process.
- Versatility: Taking into account multiple needs such as refrigeration, heating, dehumidification, and hot water supply.
- Environmental compliance: significantly reduce fossil fuel consumption and help the winery achieve low-carbon goals.
If you are interested in similar projects, we can further discuss technical details or implementation plans!